For full functionality of this site it is necessary to enable JavaScript. Here are the instructions how to enable JavaScript in your web browser.
Save to read list Published by Isabel Stagg, Editorial Assistant World Pipelines, Monday, 18 December 2023 12:00 Applied Bearings

Chris Johnson, Managing Director, SMB Bearings, UK, delves into the significance of surface preparation and coatings for Industrial bearings in pipeline applications.
According to a study published in the Journal of Loss Prevention in the Process Industries, the main causes of pipeline failures include corrosion, equipment malfunction and operational errors. These factors contribute to the need for costly repairs and downtime, further highlighting the importance of proactive maintenance and reliable equipment.
Industrial bearings serve as vital components in pipelines, facilitating the smooth and efficient flow of oil, gas and various fluids. However, these bearings are susceptible to damage caused by friction, corrosion and wear – factors that can result in costly downtime and repairs for operators of oil and gas pipelines.
Meanwhile, a survey conducted by Ernst & Young found that 60% of oil and gas executives identified unscheduled asset downtime as the biggest barrier to achieving optimal operational efficiency. This indicates that downtime and repairs pose significant challenges to the productivity and profitability of pipeline operators.
To mitigate these challenges and ensure optimal performance and durability, surface preparation and coatings for industrial bearings play a pivotal role. By exploring various surface preparation techniques and coating options, we can gain valuable insights to help pipeline operators, engineers and maintenance personnel make informed decisions when selecting the right coating solutions for their pipelines.
Surface preparation is a critical step in the coating process, as it ensures a clean and receptive surface for coatings. Three commonly used surface preparation techniques include shot blasting, grinding and cleaning.
Shot blasting involves propelling abrasive particles onto the bearing surface to remove contaminants, scale and oxide layers. This technique not only cleans the surface but also enhances its roughness, promoting better adhesion of coatings.
Grinding is another technique that removes irregularities, burrs, and imperfections from the bearing surface. By creating a smooth and uniform surface, grinding enhances the coating’s uniformity and adhesion while reducing the risk of premature coating failure.
Cleaning is essential to remove oil, grease, dust and other contaminants from the surface. Different cleaning methods, such as solvent cleaning, alkaline cleaning, and high-pressure water jetting, can be employed based on the nature and severity of the contamination. Clean surfaces are crucial for achieving proper coating adhesion and performance.
Types of coatings for industrial bearings
Various types of coatings are available to enhance the wear, corrosion, and chemical resistance of industrial bearings. The choice of coating depends on the specific requirements of the pipeline application. Some commonly used coatings include thermal spray coatings, electroplating and polymer-based coatings.
Thermal spray coatings involve depositing a molten or powdered material onto the bearing surface using a thermal spray gun. These coatings provide excellent wear resistance and can be customised with specific materials such as ceramics, metals, or alloys to suit the operating conditions. Electroplating is a process where a metal coating is deposited onto the bearing surface by electrolysis. This technique offers superior corrosion protection and can be applied with precision, allowing for controlled coating thickness and uniformity.
Polymer-based coatings offer exceptional chemical resistance and can withstand harsh operating environments. They can be tailored to provide specific properties such as low friction, high load capacity, and resistance to abrasion, making them suitable for diverse pipeline applications.
Key factors in coating selection
When selecting a coating system for industrial bearings, several factors must be considered. These include…
To access the full version of this article and get a free trial subscription to World Pipelines, sign up here!
Read the article online at: https://www.worldpipelines.com/special-reports/18122023/enhancing-pipeline-efficiency/
Embed article link: (copy the HTML code below):
This article has been tagged under the following:
This content is available to registered readers of our magazine only. Please sign in or register for free.
Register for free » Get started now for absolutely FREE, no credit card required.
Already a member? Sign in here
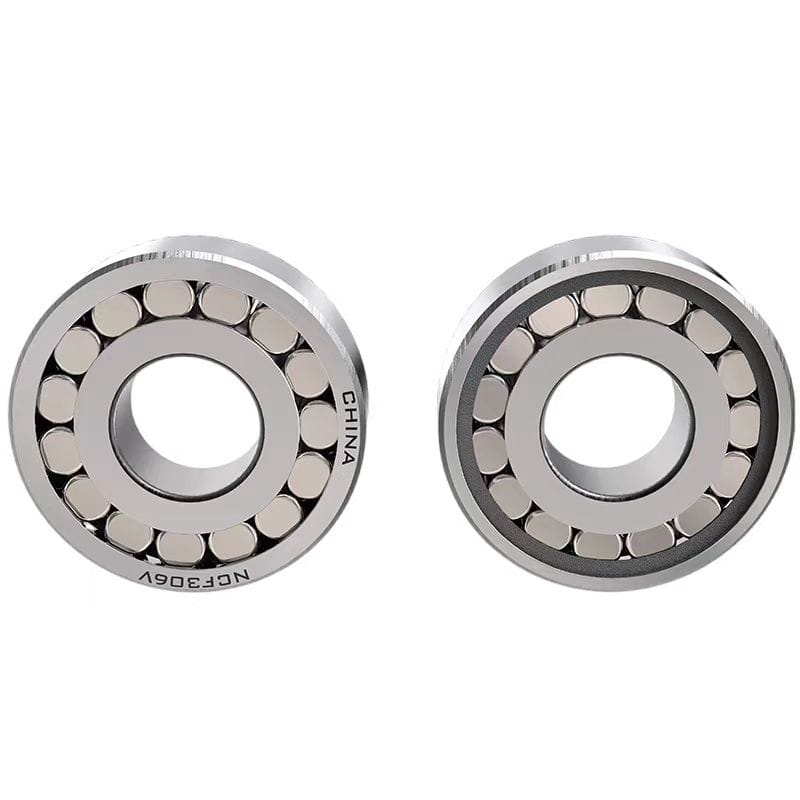
6202 Bearings Copyright © 2023 Palladian Publications Ltd. All rights reserved | Tel: +44 (0)1252 718 999 | Email: enquiries@worldpipelines.com