by Daniel Ribeiro, Product Manager, TE Connectivity
In recent years, demand for solar power has grown as a greener alternative to traditional fossil-fuel-based power generation, and the trend among solar power generation installations has been toward systems that have both a larger footprint and larger production capacity. Solar Pv Wiring Harnesses
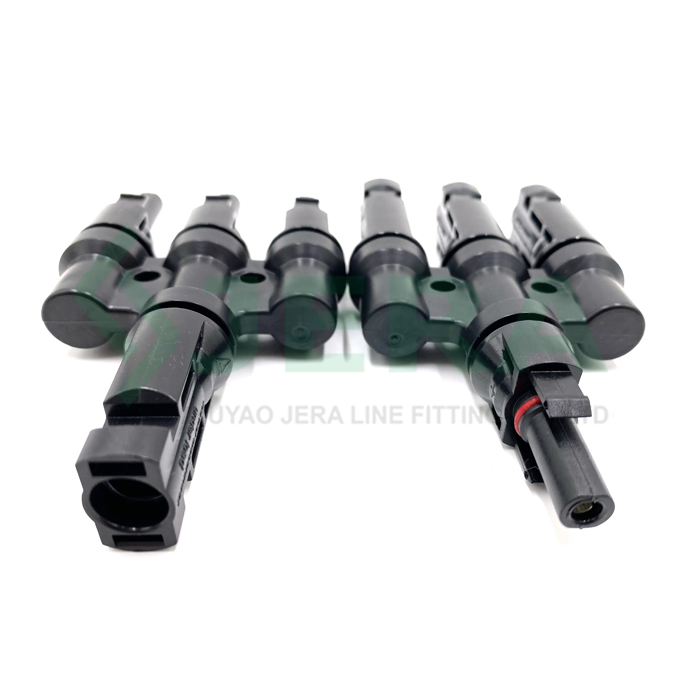
However, as solar farms continue to grow in capacity and complexity, so do the costs associated with their installation, operation and maintenance. Unless the system is properly designed, small voltage losses compound as the system size is increased. TE Connectivity’s (TE) Solar Customizable Trunk Solution (CTS) system relies on a centralized, trunk-bus architecture (discussed below). The design provides an efficient alternative to the traditional approach, which relies on hundreds or thousands of individual combiner box connections and a more complex overall wiring scheme.
TE’s Solar CTS eliminates combiner boxes by running a pair of above ground aluminum cables with the flexibility of connecting TE’s string harness with our patented Gel Solar Insulation Piercing Connector (GS-IPC) anywhere along the length of the wire. From an installation point of view, this calls for fewer cables and fewer points of connection to be established in the field.
The CTS system yields immediate savings for system owners and operators, in terms of reduced wire and cable costs, reduced installation time and faster system startup (yielding savings of 25-40% in these categories). It also enables ongoing savings over the lifecycle of the solar farm, by systematically reducing voltage losses (and thus protecting production capacity),and easing long-term maintenance and troubleshooting efforts.
The CTS design also improves overall system reliability and efficiency for operators of large-scale solar farms, by making field troubleshooting and repair efforts on-site easy. And while the system benefits from standardized and modular design concepts, it can also be customized to address different site-specific conditions and engineering considerations. An important aspect of this offering is that TE works closely with its customers to provide complete engineering support. Some of these services include voltage drop calculations, efficient system layouts, balanced inverter loading, and training for field installers.
In any traditional solar power generation system, every point of connection — regardless of how well-designed or how properly installed it is — will create some minor resistance (and thus leakage of current and voltage drop across the system). As the size of the system grows, the compounded effect of this current leakage and voltage drop grows, undermining production and financial objectives for the overall commercial-scale solar farm.
By contrast, the new streamlined trunk-bus architecture described here improves the efficacy of the DC grid network by deploying larger trunk cables with fewer connections, which provide a lower voltage drop across the entire system.
Focus on the three key components
The CTS system consists of three main components (described here):
Gel solar insulation-piercing connectors (GS-IPC). The gel solar insulation piercing connectors (GS- IPC) connect a string of photovoltaic panels to the trunk bus. The trunk bus is a large conductor which carries higher level currents (up to 500 kcmil) between the low-voltage DC network and the system DC/AC inverters.
TE’s Gel Solar Insulation Piercing Connector
The GS-IPC uses insulation-piercing technology, whereby small piercing blades penetrate the insulating jacket on the cable and establish the electrical connection to the conductor beneath the insulation. During installation, one side of the connector “bites” the large-scale cable, and the other side is the tap cable. This eliminates the need for time-consuming and labor-intensive insulation cutback or stripping by field technicians. The novel GS-IPC connector requires only a socket or impact wrench with a hexagonal socket, and each connection can be installed in under two minutes (as reported by early adopters of the novel CTS system). Installation is further simplified thanks to the use of a shear bolt head, which shears off once the pre-engineered torque is achieved and the blades of the connector have simultaneously penetrated the cable insulation and reached the conductor strands without damaging them. The GS-IPC assemblies can be used for cable sizes ranging from #10 AWG to 500 Kcmil.
Meanwhile, to protect these connections from damage from UV exposure and weather conditions, the GS-IPC connection also includes another important design element — a protective gel box enclosure that is installed on each trunk/bus network connection. Once the connector is properly installed, the field technician places and closes a cover filled with TE’s Raychem Powergel sealant. This sealant expels any moisture in the connection at time of installation and eliminates future moisture ingress for the lifetime of the connection. The gel box enclosure provides complete environmental protection by reducing current leakage, UV and sunlight resistance, and provides flame retardancy.
Overall, the GS-IPC assemblies used in the TE Solar CTS system meet stringent UL requirements for photovoltaic systems. And the GS-IPC connectors have been successfully tested in accordance with UL 486A-486B, CSA C22.2 No. 65-03, and applicable UL6703 tests as listed by Underwriters Laboratories Inc., File No. E13288.
Solar fuse harnesses (SFH). The SFH is a system of assemblies — including in-line over-molded higher rated fuses, tapping, whips and string jumpers — that can be configured to provide a pre-manufactured fuse-harness solution that is UL9703 compliant. In a traditional solar-farm array, the fuses are not located on the harness; rather, they are typically located on each combiner box. Using this newer SFH approach, the fuses are embedded on the harness instead. This provides several benefits — it aggregates multiple strings, reduces the overall number of combiner boxes needed, reduces material and labor costs, simplifies installation, and increases ongoing savings related to long-term system operation, maintenance and troubleshooting.
Trunk-disconnect boxes. The trunk-disconnect boxes that are used in the TE Solar CTS system provide load break, surge protection, and switched negative, protecting the system from surge prior to the inverter connection, and giving operators added flexibility to connect and disconnect the system, as needed. They are strategically located to minimize cabling (and without compromising the voltage drop across the system).
These disconnect boxes are constructed from either fiberglass or steel and provide up to 400 amps load break with surge and common ground capability integrated. They use shear bolt connectors for fast, easy installation, and meet UL requirements for thermal cycling, humidity and electrical cycling.
These trunk-disconnect boxes use a load break switch that was built from the ground up to be a 1500-V switch. By comparison, other solutions on the market often use a disconnect switch built from a 1000-V chassis that has been upgraded to handle 1500 V. This can result in very high heat within the disconnect box.
For added reliability, these trunk-disconnect boxes use a larger load break switch, and a larger enclosure (30” x 24” x 10”)to allow for improved heat dissipation. Similarly, these disconnect boxes can accommodate a larger bend radius for cable ranging in size from 500 AWG to 1250 kcmil.
They are UL rated from 2 AWG to 1000 kcmil conductors.
Sponsored content by TE Connectivity

Solar Cable Top Tie Copyright © 2023 WTWH Media, LLC. All Rights Reserved. Site Map | Privacy Policy | RSS